Home > Tool Steel H11 AMS 6485
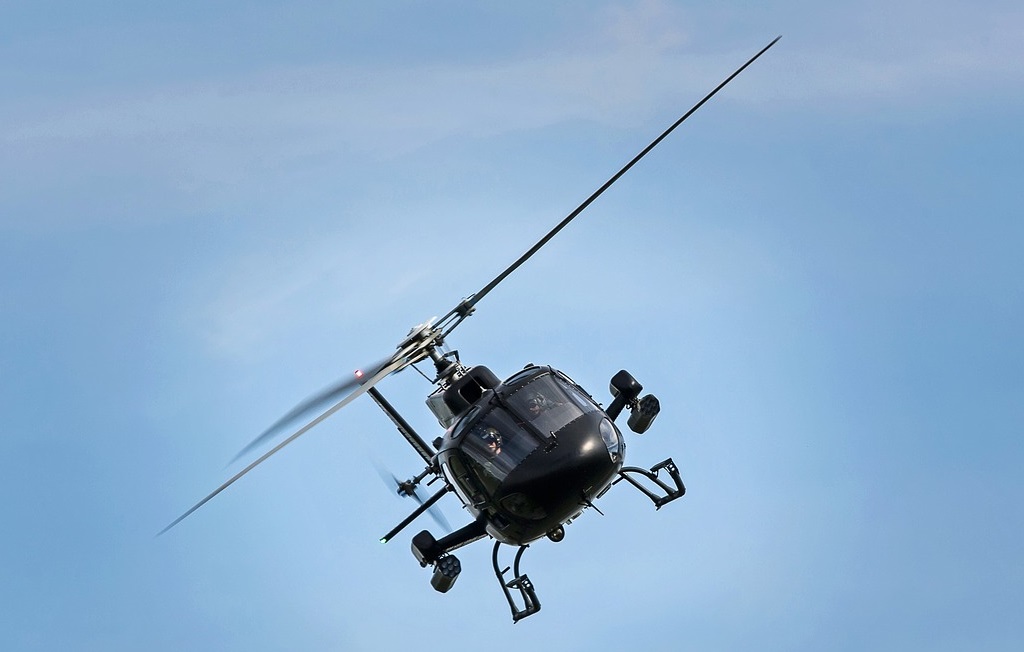
Tool Steel H11 AMS 6485
AMS 6485 is a sub-type specification of Tool Steel H11. It is available in steel bars and forgings and mostly finds use in the aerospace industry for manufacturing of parts that require exceptional impact toughness, such as aircraft landing gear, and rotors and shafts in helicopters.
Depending on the heat treatment used, AMS 6485 also finds use in hot work applications with very high loads like hot-work forging, and extrusion dies. Even though AMS 6485 isn’t characterized by outstanding wear resistance, this quality of the alloy can be improved with some heat treatments.
The standard heat treatment for AMS 6458 includes:
- Annealing – preheat at 390° F (200° C) and hold for 15 minutes. Then use step-heating method to achieve 1560° F (850° C) and hold for 2 hours. Slow-cool in the furnace until the samples reach 840° F (450° C). Open the furnace and cool to room temperature.
- Austenitizing (hardening) – heat to 500° F (260° C), then step-heat to 1500° F (815° C) and hold for 15 minutes, followed by step-heating to 1850° F (1010° C) and holding it for 30 minutes at that temperature.
- Quenching – slow-cool in the furnace for 30 minutes. Then, air-cool the parts to 150° F (65° C). In the case of oil-quenching, submerge the parts while they are at the austenitizing temperature.
- Tempering or double tempering should be done at temperatures of 840° F (450° C), 930° F (500° C), 1020° F (550° C), 1110° F (600° C), and 1200° F (650° C), depending on the combination of toughness and hardness wanted.
Products