Cobalt L-605 View AMS Numbers >
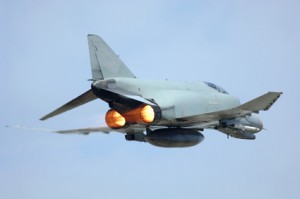
Cobalt L-605 (Alloy 25)
Cobalt L-605 (also known as alloy 25) is a cobalt-based superalloy with high levels of chromium and tungsten. It is characterized by outstanding high-temperature strength up to 1500 °F (1093 °C), excellent oxidation resistance at high temperatures up to 2000 °F (1093 °C) in corrosive environments, and superior resistance to sulfidation wear and galling. Cobalt L-605 has other less-known qualities like high ductility and biocompatibility. Cobalt L-605 is non-magnetic.
That said, like most other superalloys, Cobalt L-605 can lose its ductility when exposed to intermediate temperatures for more extended periods.
The strength of Cobalt L-605 is achieved thanks to solid-solution strengthening by tungsten in the first phase and strengthening with precipitated carbides in the second phase. Cobalt L-605 has very good forming characteristics and can be readily forged, hot-worked, or cold worked.
Thanks to all of its characteristics, Cobalt L-605 finds use in the aerospace industry. It is mainly used for manufacturing of gas turbine engine components, especially those that are often subjected to high heat. These include rings and blades for turbines, and combustion chamber parts (combustor liners).
Apart from the aerospace industry, Cobalt L-605 finds use in land-based gas turbines in power plants, and in industrial furnaces for muffles and liners in high-temperature kilns. Cobalt L-605 can also be used for manufacturing of high-temperature ball bearings and bearing races. This superalloy can also find a use for parts used in corrosive environments, mainly with wet chlorine, hydrochloric acid, and nitric acid.
Thanks to its biocompatibility, Cobalt L-605 can also be used in the medical industry, mainly for manufacturing of heart valves. That said, for these parts a special recrystallization process must be applied in order to control the grain size for a combination of strength and ductility.
Tech Steel & Materials offers Cobalt L-605 in three AMS sub-type specifications, two ASTM sub-type specifications, and multiple and customized shapes/forms:
- AMS 5537 (Foil, Plate, Sheet, and Strip)
- AMS 5759 (Bar, Forging, Ring or Custom Tube)
- AMS 5796 (Wire)
- ASTM F1091-12
- ASTM F90-14
We offer a fully customized line of tube drawing and seamless tubing for Nickel 601. To learn more about our custom tubing services click here: Custom Tubing for Your Unique Application
Chemical Composition of Cobalt L-605
Element | Min (%) | Max (%) |
Carbon, C | 0.05 | 0.15 |
Manganese, Mn | — | ≤ 2.00 |
Silicon, Si | — | ≤ 0.40 |
Sulfur, S | — | ≤ 0.015 |
Phosphorus, P | — | ≤ 0.02 |
Chromium, Cr | 19.0 | 21.0 |
Molybdenum, Mo | 1.20 | 1.40 |
Iron, Fe | — | ≤ 3.00 |
Tungsten, W | 14.0 | 16.0 |
Nickel, Ni | 9.0 | 11.0 |
Cobalt, Co | — | *Balance |
*Not exclusively to the element mentioned, but that one predominates other elements that are used only in minimal quantities.
Fabrication and Working Instructions
Cobalt L-605 is characterized by good formability and fabricability. It can be easily forged and hot worked at temperatures between 1900 °F, and 2300 °F (1038 °C to 1260 °C), or cold worked in case of bending, spinning and drawing.
However, this superalloy hardens very rapidly during working. To mitigate this, we recommend using regular annealing treatments at intermediate temperatures, especially if the end parts are very complex.
Cobalt L-605 can be readily welded using standard methods, including tungsten arc, gas metal arc, shielded metal arc, electron beam, and resistance welding. That said, even though it is doable, welding using the submerged arc welding process is not recommended. Minimum restraint and low interpass temperature are recommended for successful weld, as well as rapid cooling afterward.
Mechanical and Physical Properties
Property | Imperial | Metric |
Density | 0.335 lb/in3 | 9.27 g/cm3 |
Melting Range | 2425 – 2570 °F | 1330 – 1410 °C |
Tensile Strength | 154 ksi | 1061 MPa |
Tensile Strength, Yield 0.2% | 75 ksi | 517 MPa |
Elongation in 2 inches (50 mm) | 55 % | 55 % |
Elongation A5 | 25 % | 25 % |
Electrical Resistivity | 34.9 µΩ in | 88.6 µΩ cm |
Magnetic Permeability at 200 oersteds | 1.002 | 1.002 |
Thermal Conductivity | 65 Btu⋅in/ft2 h °F | 9.4 W/m K |
Specific Heat | 0.092 Btu/lb °F | 385 J/kg °C |
Coefficient of Thermal Expansion, RT – 200°F | 6.8 × 10-6 in/in °F | 12.3 µm/m °C |
Resistance on air (up to the temperature listed) | 1994 °F | 1090 °C |
Heat Treatment
High-temperature annealing is recommended to maintain the best properties of Cobalt L-605. Lower temperature annealing may cause carbide precipitation which is unwanted in superalloys such as Cobalt L-605. The most common annealing treatment is as follows:
- Annealing at 2150 °F to 2250 °F (1176 °C to 1232 °C)
- Rapid air cooling or water quenching
Select AMS Number:
AMS Number | Alloy | Type | UNS | Cross Ref. Spec | Misc./Shape | |
---|---|---|---|---|---|---|
AMS 5537 Foil | L-605 | Cobalt | R30605 | - | Foil |
![]() |
AMS 5537 Plate | L-605 | Cobalt | R30605 | - | Plate |
![]() |
AMS 5537 Sheet | L-605 | Cobalt | R30605 | - | Sheet |
![]() |
AMS 5537 Strip | L-605 | Cobalt | R30605 | - | Strip |
![]() |
AMS 5759 Bar | L-605 | Cobalt | R30605 | - | Bar |
![]() |
AMS 5759 Custom Tube | L-605 | Cobalt | R30605 | - | Custom Tube |
![]() |
AMS 5759 Forging | L-605 | Cobalt | R30605 | - | Forging |
![]() |
AMS 5759 Ring | L-605 | Cobalt | R30605 | - | Ring |
![]() |
AMS 5796 |
L-605 | Cobalt | R30605 | - | Wire |
![]() |
Select ASTM Number:
ASTM Specification | Alloy | Type | UNS | Cross Ref. Spec |
---|---|---|---|---|
ASTM F1091-12 | L-605 | Cobalt | UNS R30605 | AMS 5537, AMS 5759, AMS 5796 |
ASTM F90-14 | L-605 | Cobalt | UNS R30605 | AMS 5537, AMS 5759, AMS 5796 |