Magnesium AZ31B 0 View AMS Numbers >
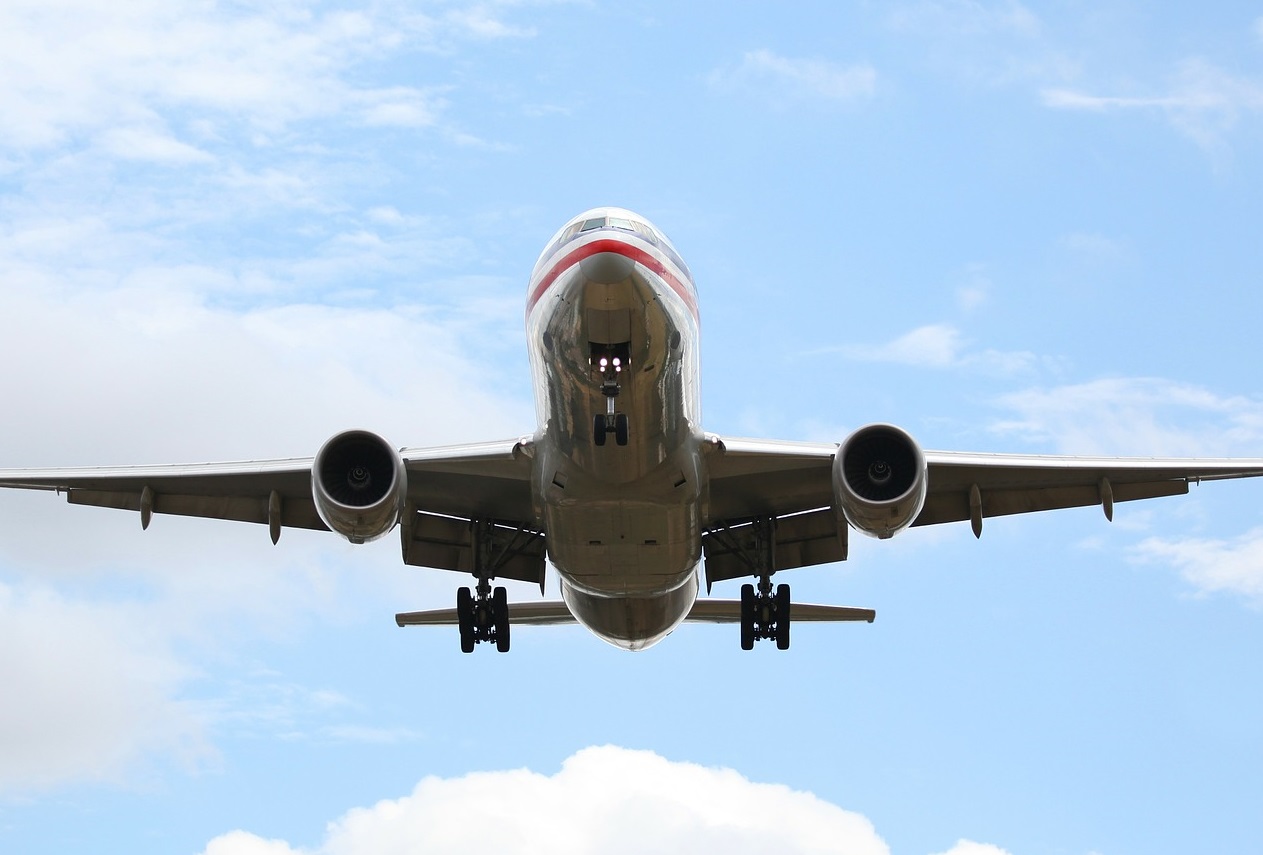
Magnesium AZ31B 0
AZ31B 0 is a magnesium alloy with high levels of aluminum and zinc. It was developed to satisfy the needs of aircraft and car manufacturers for more fuel-efficient and eco-friendly vehicles. Magnesium AZ31B 0 is much lighter than comparable steel alloys, and it also has much better strength to weight ration than aluminum alloys of the same grade. Parts made from this alloy are also very stiff, which makes it a great choice for structural components in the aerospace industry. Magnesium AZ31B 0 is also highly recyclable, which is another advantage it has over other alloys.
Overall, AZ31B 0 has very good strength and ductility at room temperature, together with high corrosion resistance and weldability. Thanks to its outstanding strength to weight ratio, this magnesium alloy is mostly used for manufacturing of aircraft fuselages. However, some premium electronics manufacturers also use AZ31B 0 for manufacturing of strong smartphone and laptop cases, and also for speaker cones in high-end audio gear due to the fact that magnesium is non-magnetic.
Car manufacturers use magnesium AZ31B 0 for manufacturing of lightweight and strong components, such as supercar or racing car wheels, thanks to the ability of the alloy to absorb vibration. On top of that, plates from this magnesium alloy are also used for manufacturing of very complex parts thanks to its outstanding dimensional stability.
That said, considering the fact that this alloy consists mostly of magnesium, it is very flammable, especially chips and powder emerged from machining or cutting. Due to the fact that magnesium can be irritating to the human body, special care should also be aimed towards good protection of the skin, eyes, and airways, in order to minimize exposure. High doses of oxide fumes of magnesium can also cause metal fume fever if inhaled.
To minimize magnesium exposure, make sure that you mostly work with large solid forms of AZ31B 0. Magnesium is hazardous only when dust or fumes are created during machining, grinding, melting, or welding.
In its raw farm, magnesium AZ31B 0 is also not very resistant to corrosion. However, the AMS 4375 specification it is offered in is anodized and is considered to have very good resistance to corrosion.
Tech Steel & Materials offers Magnesium AZ31B 0 in one sub-type specifications and two shapes/forms:
- AMS 4375 (Plate and Sheet)
Chemical Composition of Magnesium AZ31B 0
Element | min | max |
Calcium, Ca | — | 0.002 |
Manganese, Mn | 0.2 | 0.4 |
Aluminum, Al | 2.7 | 3.1 |
Copper, Cu | — | 0.003 |
Iron, Fe | — | 0.005 |
Zinc, Zn | 0.7 | 0.9 |
Magnesium, Mg | — | *Balance |
*Not exclusively to the element mentioned, but that one predominates other elements that are used only in minimal quantities.
Fabrication and Working Instructions
Apart from the fact that special care must be taken while machining (magnesium fire arresting kit is required), Magnesium AZ31B 0 is considered to be very easy to machine using a lubricant. AZ31B 0 can be easily formed if preheated to 500° F (260° C). Magnesium AZ31B is also easily welded using metal arc and gas tungsten arc welding processes. The welded parts are of very high strength.
Mechanical and Physical Properties
Property | Imperial | Metric |
Density | 0.0639 lb/in³ | 1.77 g/cc |
Tensile Strength | 37.7 ksi | 260 MPa |
Yield Strength at 0.2% Offset | 29.0 ksi | 200 MPa |
Compressive Yield Strength at 0.2% Offset | 14.1 ksi | 97 MPa |
Ultimate Bearing Strength | 55.8 ksi | 385 MPa |
Bearing Yield Strength | 33.4 ksi | 230 MPa |
Shear Strength | 18.9 ksi | 130 MPa |
Shear Modulus | 2470 ksi | 17 GPa |
Modulus of Elasticity | 6498 ksi | 44.8 GPa |
Poisson’s Ration | 0.35 | 0.35 |
Elongation in 4D | 15% | 15% |
Charpy Impact (V-Notch) | 3.17 ft-lb | 4.30 J |
Hardness, Brinell | 49 | 49 |
Thermal Properties
Property | Imperial | Metric |
Thermal Expansion Coefficient at 32-212° F (0-100° C) | 14.4 µin/in°F | 26 µm/m°C |
Thermal Conductivity | 666 BTU in/hr.ft².°F | 96 W/mK |
Heat Treatment
Magnesium AZ31B 0 can be heat treated using the following process:
- Stress relief is done at a temperature of 300° F (149° C) for 30 to 60 minutes, followed by air cooling to room temperature.
- Annealing is done at a temperature of 650° F (344° C), followed by gradually cooling the part in the furnace where it was heated.
Select AMS Number:
AMS Number | Alloy | Type | UNS | Cross Ref. Spec | Misc./Shape | |
---|---|---|---|---|---|---|
AMS 4375 Plate | AZ31B 0 | Magnesium | M11311 | QQ-M-44 | Plate |
![]() |
AMS 4375 Sheet | AZ31B 0 | Magnesium | M11311 | QQ-M-44 | Sheet |
![]() |