Steel Custom 455 View AMS Numbers >
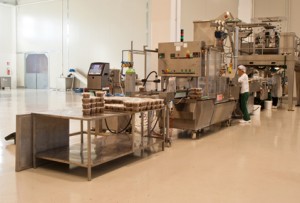
Stainless Steel Custom 455
Stainless Steel Custom 455 is age-hardenable martensitic steel with many favorable properties, including excellent formability and machinability (hot and cold), high yield strength and toughness, excellent corrosion resistance to atmospheric environments, age-hardenability with only one treatment, and good ductility.
As a result, Custom 455 is used in various fields, including medical devices and instruments, needles, pins, food processing and handling, and heat exchangers and conveyors.
Tech Steel & Materials offers Stainless Steel Custom 455 in two four-type specifications and multiple shapes/forms:
- AMS 5578 (Tubing)
- AMS 5617 (Bar, Forging, and Wire)
- AMS 5672 (Wire)
- AMS 5860 (Plate, Sheet, and Strip)
Stainless Steel Custom 455 Chemical Composition
Element | Min (%) | Max (%) |
Carbon, C | — | 0.05 |
Manganese, Mn | — | 0.50 |
Silicon, Si | — | 0.50 |
Sulfur, S | — | 0.03 |
Phosphorus, P | — | 0.04 |
Chromium, Cr | 11 | 12.5 |
Niobium + Tantalum, Nb + Ta | 0.1 | 0.5 |
Nickel, Ni | 7.5 | 9.5 |
Copper, Cu | 1.5 | 2.5 |
Molybdenum, Mo | — | 0.5 |
Titanium, Ti | 0.8 | 1.4 |
Iron, Fe | — | *Balance |
*Not exclusively to the element mentioned, but that one predominates other elements that are used in smaller quantities.
Fabrication and Working Instructions
Stainless Steel Custom 455 reacts well to hot working and cold working. For hot working, temperatures ranging from 1650 to 2300 °F (899 to 1260 °C) are recommended. To obtain optimal mechanical properties, before forging, the alloy should be heated uniformly to temperatures ranging from 1900 to 2100 °F (1038 to 1149 °C). Furthermore, for optimal grain size, a finishing temperature ranging from 1500 to 1700 °F (816 to 927 °C) is recommended.
Although Custom 455 is martensitic steel with exceptional toughness and yield strength, it possesses excellent ductility and formability. Thus, the material reacts very well to cold working in the annealed condition. Specifically, it responds well to forming, cold drawing, and cold rolling, without intermediate annealing. Moreover, Custom 455 also reacts well to cold-heading and warm-heading operations.
Custom 455 can also be finished in very tight tolerances when in an annealed state, thanks to the minimal -0.001 in/in change during hardening.
However, it’s always best to form or machine the material before heat treatment since it elevates the strength and toughness even further.
Physical Properties Stainless Steel Custom 455
Property | Imperial | Metric |
Specific Density (annealed condition) | 0.280 lb/in3 | 7.76 g/cm3 |
Specific Density (H 900) | 0.281 lb/in3 | 7.78 g/cm3 |
Specific Density (H 950) | 0.281 lb/in3 | 7.79 g/cm3 |
Specific Density (H 1000) | 0.282 lb/in3 | 7.80 g/cm3 |
Specific Density (H 1050) | 0.282 lb/in3 | 7.80 g/cm3 |
Specific Density (H 1100) | 0.283 lb/in3 | 7.82 g/cm3 |
Electrical Resistivity (annealed condition) | 35.6 µΩ in | 90.6 µΩ cm |
Electrical Resistivity (H 950) | 29.8 µΩ in | 75.8 µΩ cm |
Mean Coefficient of Thermal Expansion (72 °F to 200 °F) (22 °C to 93 °C) | 5.9 [10-6/°F] | 10.6 [10-6/K] |
Mean Coefficient of Thermal Expansion (72 °F to 300 °F) (22 °C to 149 °C) | 6.03 [in/in/°F·106] | 10.9 [10-6/K] |
Mean Coefficient of Thermal Expansion (72 °F to 500 °F) (22°C to 260°C) | 6.2 [10-6/°F] | 11.2 [10-6/K] |
Mean Coefficient of Thermal Expansion (72 °F to 700 °F) (22 °C to 371 °C) | 6.45 [10-6/°F] | 11.6 [10-6/K] |
Mean Coefficient of Thermal Expansion (72 °F to 900 °F) (22 °C to 482 °C) | 6.68 [10-6/°F] | 12 [10-6/K] |
Thermal Conductivity (@ 212 °F) (@ 100 °C) | 125 Btu/(hr/ft²/in/°F) | 216 [W/m-K] |
Thermal Conductivity (@ 392 °F) (@ 200 °C) | 137 Btu/(hr/ft²/in/°F) | 237 [W/m-K] |
Thermal Conductivity (@ 572 °F) (@ 300 °C) | 148 Btu/(hr/ft²/in/°F) | 256 [W/m-K] |
Thermal Conductivity (@ 752 °F) (@ 500 °C) | 162 Btu/(hr/ft²/in/°F) | 280 [W/m-K] |
Thermal Conductivity (@ 932 °F) (@ 600 °C) | 172 Btu/(hr/ft²/in/°F) | 297 [W/m-K] |
Poisson’s Ratio (H900 Condition) | 0.300 | 0.300 |
Modulus of Elasticity (H900 Condition) | 29 x 106 ksi | 200 x 103 MPa |
Modulus of Rigidity | 11 x 103 ksi | 76 x 103 MPa |
Stainless Steel Custom 455 Mechanical Properties
Property | Imperial | Metric |
Ultimate Tensile Strength | 245000 psi | 1689 MPa |
Ultimate Tensile Strength (@800 °F / 427 °C) | 180000 psi | 1241 MPa |
Yield Strength (0.02% Offset) | 237000 psi | 1634 MPa |
Yield Strength (0.02% Offset, @800 °F / 427 °C) | 166000 psi | 1145 MPa |
Elongation at Break (in 4D) | 11% | 11% |
Rockwell Hardness C | 49 | 49 |
Brinell Hardness | 472 | 472 |
Knoop Hardness | 519 | 519 |
Vickers Hardness | 496 | 496 |
Charpy Impact | 8.85 ft-lb | 12 J |
Shear Modulus | 112000 ksi | 76.9 GPa |
Heat Treatment
Stainless Steel Custom 455 comes in the annealed condition unless specified otherwise. However, depending on the needs, additional heat treatment will yield different hardness and strength levels. The H 900, H 950, H 100, H 1050, and H 1100 are all precipitation or age-hardened versions of the alloy.
The number refers to the temperature used for age hardening. For example, Custom 455 H 900 is first annealed, then heated to 900°F / 480°C and air-cooled for four hours.
Select AMS Number:
AMS Number | Alloy | Type | UNS | Cross Ref. Spec | Misc./Shape | |
---|---|---|---|---|---|---|
AMS 5578 |
Custom 455 | Stainless Steel | S45500 | - | Tubing |
![]() |
AMS 5617 Bar | Custom 455 | Steel | S45500 | - | Bar |
![]() |
AMS 5617 Forging | Custom 455 | Steel | S45500 | - | Forging |
![]() |
AMS 5617 Wire | Custom 455 | Steel | S45500 | - | Wire |
![]() |
AMS 5672 |
Custom 455 | Steel | S45500 | - | Wire |
![]() |
AMS 5860 Plate | Custom 455 | Stainless Steel | s45500 | - | Plate |
![]() |
AMS 5860 Sheet | Custom 455 | Stainless Steel | s45500 | - | Sheet |
![]() |
AMS 5860 Strip | Custom 455 | Stainless Steel | s45500 | - | Strip |
![]() |