Steel M-50 View AMS Numbers >
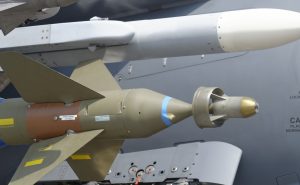
Steel M-50
Steel M-50 is a high-speed premium-melted alloy with a high level of molybdenum. It has high compressive strength at elevated temperatures, as well as outstanding resistance to multi-axial stresses, good fatigue strength, and good resistance to oxidation. Steel M-50 also has high levels of cleanliness and can be finished to a high luster.
Thanks to these properties of Steel M-50, it is primarily used for manufacturing of aircraft engine bearings, bearings for gas turbines, parts for missiles, and other applications that require high wear resistance and strength up to 800° F (425° C).
Steel M-50 can also be used for manufacturing of high-performance tools such as high-speed drill bars, vibration and impact tools, deep drawing and punching die, metal cutting saw blades, cold heading, and extrusion tools. Please note that Steel M-50 doesn’t have high abrasion resistance and should be used for tooling applications where that property is not essential like woodwork or commercial twist drills.
This steel alloy is produced using VIM-VAR process, or vacuum induction melting followed by vacuum arc remelting (VAC-ARC). Parts made with the VIM-VAR process have excellent micro cleanliness and superior fatigue resistance.
Tech Steel & Materials offers Steel M-50 in two sub-type specifications and three shapes/forms:
Chemical Composition of Steel M-50
Element | min | max |
Carbon (C) | 0.78 | 0.88 |
Manganese (Mn) | 0.15 | 0.45 |
Silicon (Si) | 0.20 | 0.60 |
Phosphorus (P) | — | 0.030 |
Sulfur (S) | — | 0.030 |
Chromium (Cr) | 3.75 | 4.50 |
Nickel (Ni) | — | 0.30 |
Molybdenum (Mo) | 3.90 | 4.75 |
Vanadium (V) | 0.80 | 1.25 |
Iron (Fe) | — | *Balance |
*Not exclusively to the element mentioned, but that one predominates other elements that are used only in minimal quantities.
Technical Data
Property | Value (imperial) | Value (metric) |
Ultimate Tensile Strength | 363-391 [psix10^3] | 2500-2700 MPa |
Hardness | — | 60-65 HRC |
Service temperature | 32-797°F | 0-425°C |
Physical, Mechanical, Thermal, Electric and Mechanical Properties of Steel M-50
Property | Type | Value |
Density | Physical | 7.85 g/cm3 / 0.283 lb /in3 |
Young’s modulus | Mechanical | 210 GPa |
Specific heat | Thermal | 460 J/kg-K |
Coefficient of linear thermal expansion | Thermal | 11.4 10^-6/ºC |
Thermal conductivity | Thermal | 25.0 W/(m·K) |
Electric resistivity | Electric | 600 Ω*m*10^-9 |
Relative magnetic permeability | Magnetic | >500 |
Coefficient of Thermal Expansion
Temperature Range | Value (Imperial) | Value (Metric) |
70-200°F (21-93°C) | 6.23 micro in/in- °F | 11.21 micro m/m- °K |
70-400°F (21-204°C) | 6.58 micro in/in- °F | 11.84 micro m/m- °K |
70-600°F (21-316°C) | 6.83 micro in/in- °F | 12.29 micro m/m- °K |
70-800°F (21-427°C) | 7.05 micro in/in- °F | 12.69 micro m/m- °K |
70-1000° F (21-538°C) | 7.38 micro in/in- °F | 13.28 micro m/m- °K |
Fabrication and Working Instructions
Steel M-50 possesses good machinability. Nonetheless, it is recommended that it is machined in the annealed condition. Steel M-50 responds well to forging, which can be carried out by slowly heating the part to 1500° F (815° C) and keep at that temperature for few hours or to heat the piece thoroughly. Then, the temperature should be increased to 2000° F (1090° C) prior to working. Forging should never be carried out below 1800° F (980° C). After forming is completed, cool slowly to room temperature.
Heat Treatment
Steel M-50 can be obtained in the annealed or hardened state, depending on the sub-specification.
Annealing is carried out at 1600° F (870° C), followed by cooling slowly to room temperature. Please note that Steel M-50 is susceptible to decarburization, which is not a wanted property given its use in tools and bearings. To mitigate decarburization, use inert or reduced-pressure atmosphere during the annealing process.
Hardening should be carried out after annealing. To properly harden Steel M-50, preheat the part to 1500° F (815° C) until the whole component is heated correctly. After preheating, increase the temperature to 2000° F (1090° C) for superheating. As with the preheating step, ensure that the whole part is heated equally before proceeding to immediate quenching in salt bath furnace or controlled atmosphere furnace. After the part was cooled using the quenching method, cool the piece to -100° F (-73° C) for 1 hour.
Tempering should be done immediately after quenching, with double tempering at 1025° F (550° C) recommended for achieving the best properties.
Select AMS Number:
AMS Number | Alloy | Type | UNS | Cross Ref. Spec | Misc./Shape | |
---|---|---|---|---|---|---|
AMS 6490 Bar | M-50 | Steel | T11350 | - | Bar |
![]() |
AMS 6490 Forging | M-50 | Steel | T11350 | - | Forging |
![]() |
AMS 6490 Tubing | M-50 | Steel | T11350 | - | Tubing |
![]() |
AMS 6491 Bar | M-50 | Steel | T11350 | - | Bar |
![]() |
AMS 6491 Forging | M-50 | Steel | T11350 | - | Forging |
![]() |
AMS 6491 Tubing | M-50 | Steel | T11350 | - | Tubing |
![]() |