Home > Steel M-50 AMS 6491
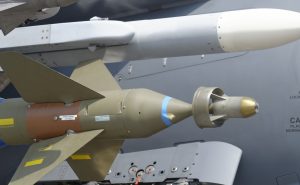
Steel M-50 AMS 6491
AMS 6491 is a sub-type specification of Steel M-50, which is a high-speed premium-melted alloy with a high level of molybdenum. Its main advantages are excellent compressive strength at elevated temperatures, outstanding resistance to multi-axial stresses, good fatigue strength, and good resistance to oxidation.
AMS 6491 is used in the aerospace industry for manufacturing of engine bearings, bearings for gas turbines and parts for missiles, and for high-speed tools such as drill bars, vibration and impact tools, deep drawing and punching die, metal cutting saw blades, cold heading, and extrusion tools.
The AMS 6491 specification of Steel M-50 is produced using a double vacuum melting process, or more precisely vacuum induction melting followed by vacuum arc remelting (VAC-ARC). The desired heat treatment of AMS 6491 is the following:
- Annealing – carried out in inert or reduced pressure atmosphere to reduce the chances of decarburization, at a temperature of 1600° F (870° C), followed by cooling slowly to room temperature.
- Hardening – this process should be done after annealing. Heat the part to 1500° F (815° C) until the whole component reaches the desired temperature. Increase the temperature to 2000° F (1090° C) for superheating and again ensure that the piece is fully heated before quenching in salt bath furnace or controlled atmosphere furnace. Cool to room temperature and then refrigerate to -100° F (-73° C) for 1 hour.
- Tempering should be carried out immediately after quenching. Double tempering at 1025° F (550° C) is recommended for achieving best properties, with triple tempering desirable in some situations.
Products