Tool Steel H11 View AMS Numbers >
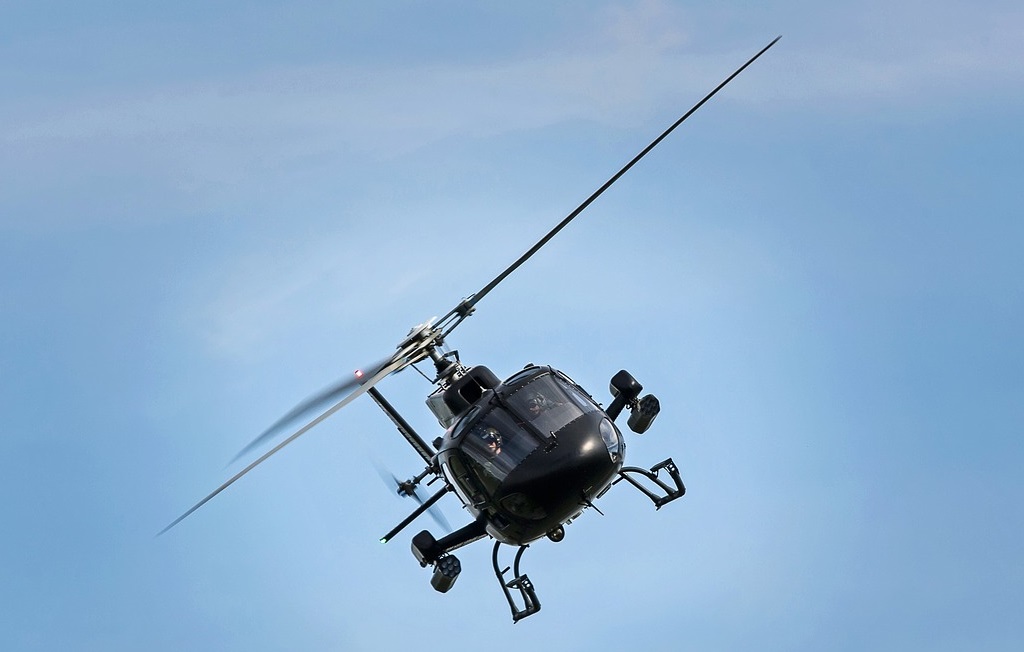
Tool Steel H11
Tool Steel H11 is a chromium-based steel alloy from the “H” family of steels according to the AISI classification system. H11 is one of the most commonly used alloys from this group, thanks to the outstanding impact toughness. Other steels from this group, such as the H13 have more vanadium, which gives better wear resistance and temper resistance, but worse impact toughness.
Thanks to these properties, Tool Steel H11 is mostly used in the aerospace industry, more precisely for the landing gear. This alloy is also widely used for helicopter rotor blades and shafts, as well as die-casting dies.
Tool Steel H11 is also used for hot tooling applications thanks to its excellent resistance to cracking, including thermal fatigue cracking, gross cracking and thermal shock during water cooling. These include hot punches, die casting dies, forging dies, hot shear blades, hot gripper dies, and extrusion tooling. Like most steels with high toughness and low carbon content, Steel H11 can be used for producing hot-work steels with the water-cooling method.
Tool Steel H11 has minimal distortion during deep-hardening and air-hardening thanks to the balanced alloy content. H11 can also be hardened with an air quenching method.
Tech Steel & Materials offers Tool Steel H11 in four sub-type specifications and multiple shapes/forms:
- AMS 6437 (Plate, Sheet, and Strip)
- AMS 6485 (Bar and Forging)
- AMS 6487 (Bar and Forging)
- AMS 6488 (Bar and Forging)
Chemical Composition of Tool Steel H11
Element | Min (%) | Max (%) |
Carbon, C | 0.38 | 0.43 |
Manganese, Mn | 0.20 | 0.40 |
Silicon, Si | 0.80 | 1.00 |
Sulfur, S | – | 0.015 |
Phosphorus, P | – | 0.015 |
Chromium, Cr | 4.75 | 5.25 |
Molybdenum, Mo | 1.20 | 1.40 |
Vanadium, V | 0.40 | 0.60 |
Nickel, Ni | – | 0.25 |
Copper, Cu | – | 0.35 |
Iron, Fe | – | *Balance |
*Not exclusively to the element mentioned, but that one predominates other elements that are used only in minimal quantities.
Fabrication and Working Instructions
Tool Steel H11 can be easily formed using conventional methods for machining and forging. For forging the preferred temperature is 2050° F (1121° C), with 1650° F (899° C) being the lowest recommended point. H11 can also be cold-worked and welded with conventional methods for steels in this group. That said, machinability of H11 is 75% to that of steels in the “W” group.
Mechanical and Physical Properties of Tool Steel H11
Property | Imperial | Metric |
Density | 0.282 lb/in³ | 7.81 g/cc |
Melting Point | 2600°F | 1427°C |
Tensile Strength | 260 ksi | 1792 MPa |
Tensile Strength, Yield | 215 ksi | 1482 MPa |
Elongation in 4D | 8 % | 8 % |
Reduction of Area | 30 % | 30 % |
Hardness, Rockwell C Air cooled from 1800°F (982°C) for 45 minutes) |
52.5 | 52.5 |
Hardness, Rockwell C Air cooled from 1850°F (1010°C) for 45 minutes) |
56 | 56 |
Hardness, Rockwell C Air cooled from 1900°F (1038°C) for 45 minutes) |
57 | 57 |
Charpy impact V-notch; air-cooled from 1850°F (1010°C) and then tempered at 535°C |
10.0 ft-lb | 13.6 J |
Charpy impact V-notch; air-cooled from 1850°F (1010°C) and then tempered at 1200°F (650°C) |
20.0 ft-lb | 27.1 J |
Charpy impact V-notch; air-cooled from 1850°F (1010°C) and then tempered at 700°F (370°C) |
25.0 ft-lb | 33.9 J |
Poisson’s Ration | 0.27 – 0.30 | 0.27 – 0.30 |
Machinability (relative rating for 1% Carbon Steel) | 75-80 % | 75-80 % |
Transverse Tensile Properties
Property | Imperial | Metric |
Tensile Strength | 260 ksi | 1792 MPa |
Tensile Strength, Yield (0.2% Offset) | 215 ksi | 1482 MPa |
Individual Value | 6 % | 6 % |
Average Value | 15 % | 15 % |
Thermal Properties of Tool Steel H11
Property | Imperial | Metric |
Thermal Expansion (at the temperature range of 68-112° F / 20-100° C) |
6.63 µin/in°F | 11.9 x 10-6/ºC |
Thermal Conductivity(at 212° F / 100° C) | 292.9 in/hr.ft².°F | 42.2 W/mK |
Heat Treatment of Tool Steel H11
Tool Steel H11 can be heat treated using various different schemes that give different properties. Heat treatments of this alloy usually consist of annealing, hardening/austenitizing, air and oil quenching, and single or double tempering at temperatures of 840° F (450° C), 930° F (500° C), 1020° F (550° C), 1110° F (600° C), and 1200° F (650° C).
According to some independent studies, the optimum heat treatment for a combination of hardness, toughness, yield strength, ultimate strength, and ductility include oil-quenching and double-tempering at 1020° F (550° C). Higher hardness can be achieved by oil-quenching and double tempering at 1110° F (600° C), but this can also lead to lower lead strength and very low ductility. Also, with the increase of hardness of Tool Steel H11, impact toughness decreases.
Select AMS Number:
AMS Number | Alloy | Type | UNS | Cross Ref. Spec | Misc./Shape | |
---|---|---|---|---|---|---|
AMS 6437 Plate | H11 | Tool Steel | T20811 | - | Plate |
![]() |
AMS 6437 Sheet | H11 | Tool Steel | T20811 | - | Sheet |
![]() |
AMS 6437 Strip | H11 | Tool Steel | T20811 | - | Strip |
![]() |
AMS 6485 Bar | H11 | Tool Steel | T20811 | QQ-T-750 | Bar |
![]() |
AMS 6485 Forging | H11 | Tool Steel | T20811 | QQ-T-750 | Forging |
![]() |
AMS 6487 Bar | H11 | Tool Steel | T20811 | - | Bar |
![]() |
AMS 6487 Forging | H11 | Tool Steel | T20811 | - | Forging |
![]() |
AMS 6488 Bar | H11 | Tool Steel | T20811 | - | Bar |
![]() |
AMS 6488 Forging | H11 | Tool Steel | T20811 | - | Forging |
![]() |