Magnets Increasingly An Alternative To Rare Earth Sources
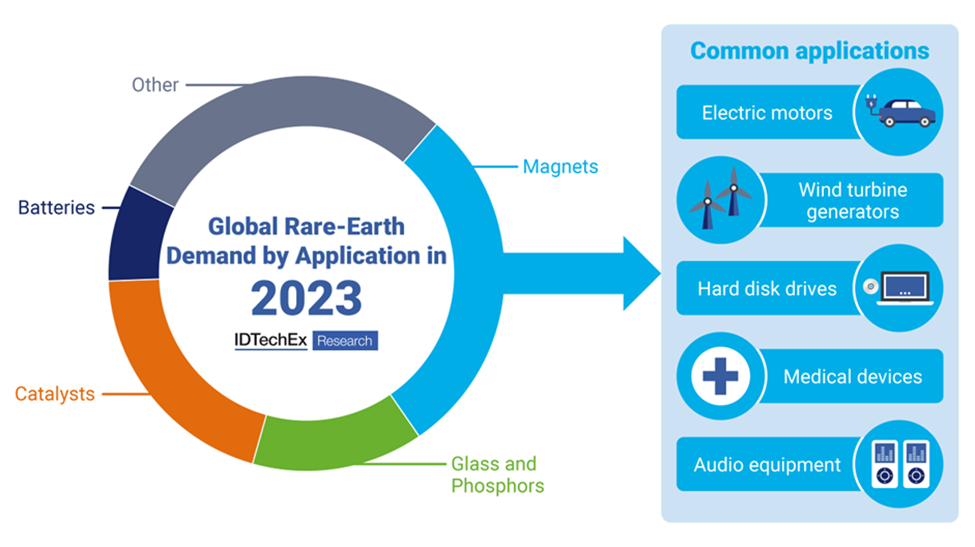
The green transition makes people aware of the growing supply risks of rare earth elements. The EU, USA, UK, Japan, New Zealand, and other regions identify rare earths as critical materials. The limited availability of primary rare earth mineral supply in many regions makes end-of-life magnets a key alternative source of critical rare earth elements.
It’s predicted that US$1.2B of critical rare earth elements may be recovered from secondary sources such as permanent magnet motors by 2045.
Rare earth permanent magnets, containing critical neodymium, praseodymium, terbium, and dysprosium elements, are used to interconvert electrical and kinetic energy.
Therefore, they are commonly employed in electric vehicle motors and wind turbine energy generators. Electric vehicles with rare earth magnet motors often provide the highest power, torque density, and efficiency, with low associated manufacturing costs, compared to other motor technologies.
China is the only country with a high regional concentration of rare earth supplies and huge refining capacity worldwide. The country processes over 90% of rare elements globally each year, particularly nearly 100% of heavy rare earth elements such as dysprosium and terbium. This situation also poses challenges in the price of key magnet materials for other countries.
To solve this, emerging companies have sought to recover neodymium, praseodymium, terbium, and dysprosium from end-of-life magnets. Long-loop recovery processes extract, separate, and recover critical rare earth from magnets into isolated rare earth oxides.
The rare earth content in permanent magnets is more than many primary mineral sources. For example, there are approximately 33% by weight of rare earths in an NdFeB magnet, including up to 31% of neodymium, while low rare earth content minerals typically mined contain around 1% by weight.
Companies like Ionic Technologies, Carester, and Shin-Etsu Chemical are developing conventional solvent extraction technologies, while ReElement uses a chromatographic separation process to recover rare earth elements from magnets with reduced solvent usage.
In addition, there’s also short-loop recovery directly to process rare earth magnets into pure recycled magnet material. Companies such as Noveon Magnetics use a high-temperature sintering process, called powder metallurgy, to recycle end-of-life magnets into new magnets that retain 84% of their original magnetic strength.
Meanwhile, HyProMag uses a hydrogen decrepitation process to extract pure NdFeB alloy from end-of-life rare earth magnets.
Comments are closed