Researchers Announce New High-Performance Titanium Alloys
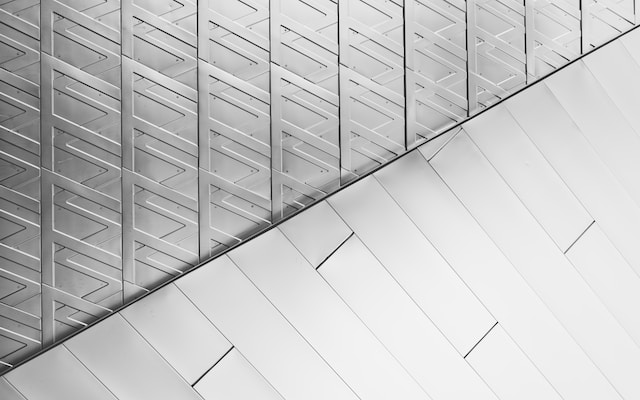
Researchers from the Hong Kong Polytechnic University (PolyU), RMIT University, and the University of Sydney have successfully used additive manufacturing, also known as 3D printing to develop high-performance titanium alloys to solve challenges associated with quality and waste management in the industrial production of titanium alloys.
By integrating alloy design, computational simulations, and experimental characterization, researchers explored the additive manufacturing process-microstructure-property space for the new titanium alloy (α–β Ti-O-Fe alloy), a new strong, ductile, and sustainable titanium alloy.
This is achieved through the incorporation of inexpensive and abundant oxygen and iron, which are the two most powerful stabilizing elements and strengtheners for α–β phase titanium alloys.
A New Titanium Alloy with Strong, Ductile, and Sustainable Characteristics
Although traditional manufacturing methods such as casting can also produce the new titanium, the poor properties of the resulting material may make it unsuitable for practical engineering. Meanwhile, additive manufacturing can effectively overcome the limitations of traditional methods to improve alloy properties.
In addition, the energy-intensive Kroll process, typically used to produce titanium alloys, generates off-grade sponge titanium, which accounts for approximately 10% of all sponge titanium, resulting in substantial waste and increased production costs.
In contrast, additive manufacturing can effectively address this problem by recycling the proportion of these off-grade sponge titanium, converting the waste into powder for use as raw material. It also means this not only can significantly lower both material and energy costs for industries but also contribute to environmental sustainability and reduce carbon footprint.
Compared with the Ti-6AI-4V benchmark material, which has been widely used since its formulation in 1954, the new titanium alloy also demonstrates better mechanical performance, with comparable ductility and considerably higher strength.
Additionally, additive manufacturing is said to allow the one-step production of complex and functional metal parts, thereby accelerating product development with reduced costs. Also, it can be used to fabricate metal parts with unique structures and compositions, which cannot be achieved using traditional methods.
Wide Application of Titanium Alloy
Nowadays, titanium alloys are advanced lightweight materials that play an indispensable role in many critical applications. It can be found in a range of sectors from aerospace to wristwatch manufacturing. Apple also has recently introduced its newest iPhone made by Titanium.
The new titanium alloy produced by the research team also exhibits immense potential for diverse applications, ranging from aerospace and marine engineering to consumer electronics and biomedical devices.
Comments are closed